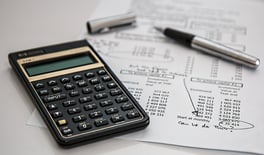
In manufacturing, there is no one-size-fits-all method for accurate forecasting.
Facing uncertainty and unique production specifications, managers must take several factors into account before forecasting any sourcing or manufacturing needs.
Below, we provide three ways manufacturers can ensure more effective forecasting to reduce costs and optimize production.
1. Determine Key Metrics
Depending on the product, manufacturers must identify one or two datasets, such as established orders or selling potential, which they see as being most valuable. By diving into industry-specific data, managers can gain insights into how many employees to hire, what materials to order and how to streamline production.
While some companies find historical trends useful for effective forecasting, some rely heavily on current market trends and real-time data. Either way, the data should be valuable throughout the entire supply chain. It’s important to not only determine what data to collect, but also how to collect it before selecting a forecasting method.
2. Consider the Reach of Your Forecasts
To effectively forecast production and sourcing needs, consider the lifecycle of products as well as how far in advance to determine future forecasts. Forecasts that reach only a few months into the future are typically more accurate than those reaching longer spans. Additionally, forecasting methods should take into consideration:
- Allowance tolerances.
- Business model.
- Company size.
- Demand trends.
- Geographic location.
Historical data can be used determine future forecasts and becomes more effective as more data is accumulated. However, the best forecasting method for specific company needs is dependent on the level of support and data they have access to.
3. Plan Ahead to Hedge Uncertainty
Several factors can interrupt the supply chain, making it difficult to accurately forecast production needs. To hedge uncertainty, consider taking the following actions:
- Consider any bottlenecks, such as materials with longer lead times, and work around obstacles that may hinder productivity.
- Schedule periodic shipments of materials to ensure sufficient supplies for production and a continuous pipeline.
- Staff the appropriate personnel and provide sufficient training to ensure employees are competent and production flows smoothly.
- Take inventory of specialized equipment, which may be difficult to operate, and allow enough time for special training.
Interested in learning more about how Hynes can help your bottom line? Contact Hynes Industries to find out how you can start reducing costs and eliminating waste today.